How do Manntech building maintenance units improve the efficiency of cleaning cycles?
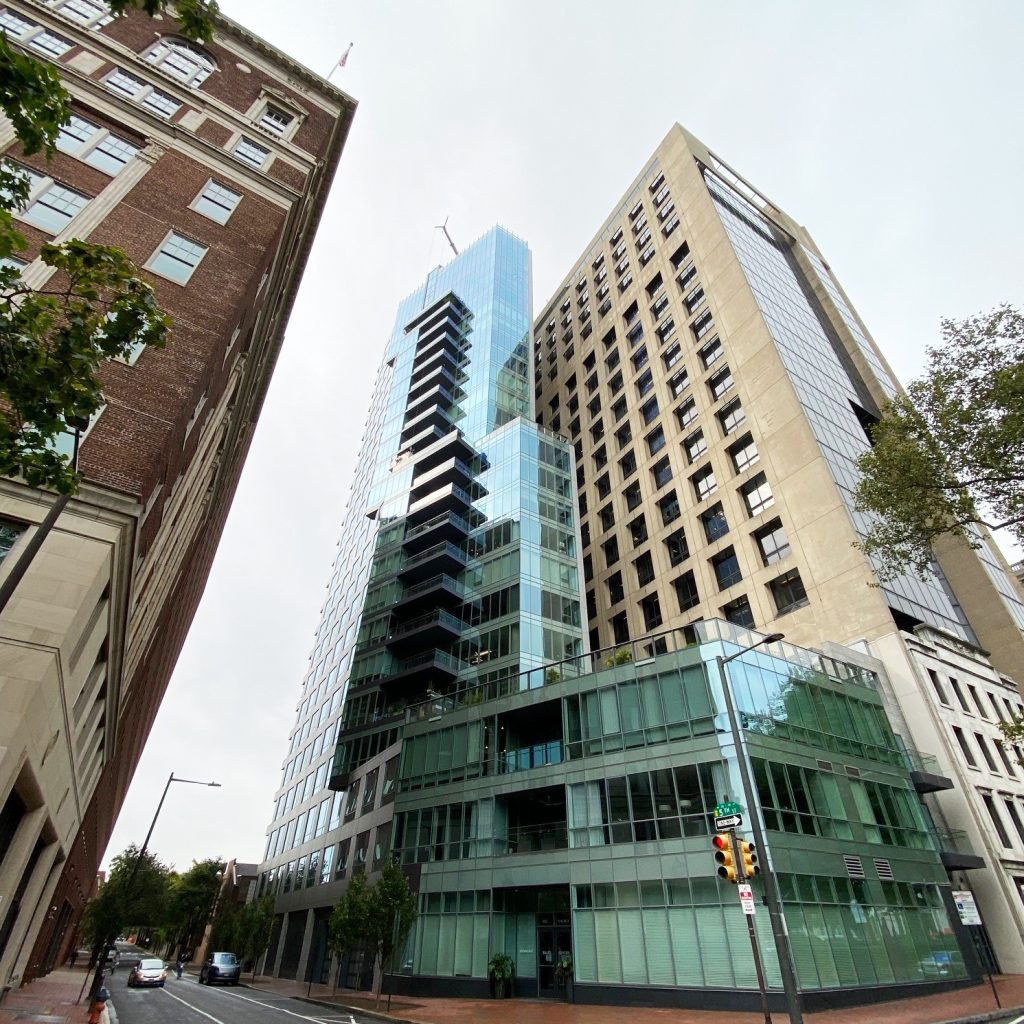
Managing the appearance of a building through a reliable and precision built maintenance system is often a priority for architects looking to preserve the aesthetic integrity of their designs.
Throughout the process of developing a custom building maintenance unit (BMU), Manntech considers the efficiency and functionality required to deliver the optimal facade access solution. Part of this consideration is the frequency and regularity of cleaning cycles that may be needed to keep a building pristine.
As a major factor in the design of a building maintenance unit, the facade maintenance cycle time is considered by Manntech engineers early in the consultation and design process. The facade maintenance cycle time is the length of time it would take for the system to complete an entire cycle of the whole facade surface area. This can vary greatly depending on the requirements of the stakeholders, the type of building, the form of the building as well as weather conditions and the local climate. Building managers and owners may prioritise more frequent cleaning cycles for the lower floors of a building as these are the most visible to the public at street level. Facade concepts that are designed to feature or reflect sunlight to enhance their grandeur may also benefit from frequent cleaning cycles so as not to allow dirt or dust to impact the visual presence of the building.
Working with Manntech to develop a custom building maintenance system grants clients access to industry-leading innovation, a wealth of experience and pioneering technology, all of which is utilised to provide precision facade access and meet cleaning needs with maximum efficiency. Buildings that feature more structurally complex designs often require multiple building maintenance units to achieve access across the entirety of the facade for comprehensive cleaning cycles.
Manntech designs and manufactures building maintenance units based on state-of-the-art engineering and technology to offer the flexibility and functionality to achieve 100% facade access often with just one building maintenance unit. The Manntech BMU at the Four Seasons in Miami, for example, delivers access to the entirety of the building’s 63-metre facade. Utilising a four-wheel design, the BMU at the Four Seasons facilitates easy and convenient transport to various drop points around the entire perimeter, while an additional material hoist provides functionality for vital maintenance tasks involving heavy lifting such as glass panel replacement.
When developing a building maintenance unit it is important to consider the value of a highly-engineered custom building access system designed to meet the exact requirements of the building over the use of abseilers. The use of rope access presents a number of drawbacks. Substantial maintenance work, such as glass replacement, is virtually impossible to complete whilst abseiling due to the weight and size of glass panels. This often prevents a proactive approach limiting essential maintenance exclusively to repair work. The addition of a building maintenance unit on a high-rise building allows for inspections, risk assessments and maintenance work to be carried out without incurring the costs of scaffolding and cranes resulting in a significantly more efficient operation.
Get in touch with the expert engineers at Manntech to discuss how a custom building maintenance unit can facilitate more efficient cleaning cycles.